The crucial thing here is continuous onsite support before development, while development, and sometimes after it. Firstly, it’s essential to invite the IoT ecosystem design team to research the production, and secondly, you need to organize their close cooperation with the production staff. It is possible to make joint decisions because no one knows the environment better than employees.
Smart Manufacturing Gives a New Round for Flexible Systems
Flexibility is one of the main vectors where manufacturing is striving today. It tangibly suffers from the traditional approach for industrial automation. The implementation of any additional feature is rather complicated here and brings about significant expenses. For industrial “big fish”, this might be less relevant in general. However, the need to reshore the factories that have recently appeared, forces even major companies to automate their manufacturing more than before to avoid large expenses. The demand for flexibility appears as well as it helps mitigate risks.
Medium and small enterprises are especially sensitive to changes in the global and local arenas. They are forced to adjust to the new business environment, sometimes immediately, to repurpose or expand their production. For most SMEs, the need for flexibility is a matter of business perspective, because it allows them the ability to produce more diverse orders, different models, components, etc.
Thus, many factors have shaped the next priority, relevant for different types of companies – to ensure the flexibility of the production process and the capabilities of production equipment. Fortunately, now we have IoT that leads to Smart Manufacturing and allows us to get Flexible Manufacturing Systems quickly and conveniently integrated and upgraded.
Smart Manufacturing is Always Flexible
Flexibility in manufacturing reflects its ability to adapt to expected and unexpected changes in the type and quantity of the product without extra-spendings. It is based on the following features:
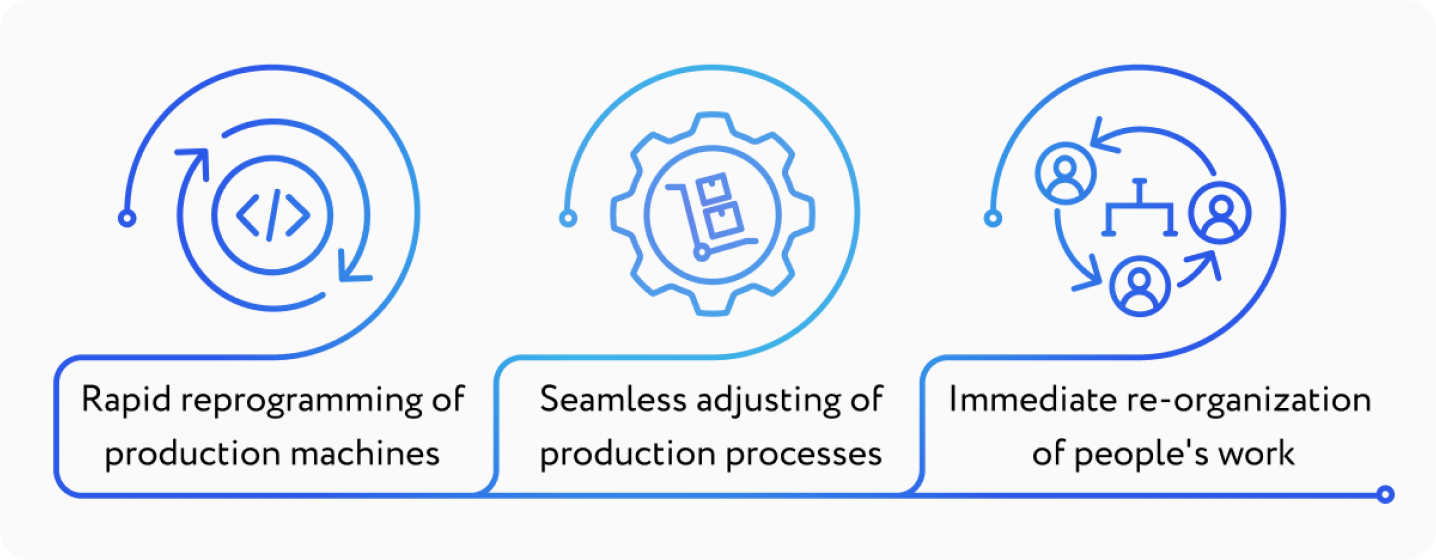
Optimization for any of the points above is already a step towards greater flexibility. Traditionally, manufacturing has reached this through Flexible Manufacturing Systems. Consisting of a production machine, material handling system, and central computer. The system allows for quick programming to easily change the parameters of the final products, and their quantity, thereby ensuring a greater yield of a variety of products. This brings substantial flexibility to the production process, which allows for saving time and money approximately twice.
What has changed with the advent of IoT? Firstly, the availability of manufacturing systems has increased. Secondly, IoT power can cover the entire enterprise and connect various systems with each other in a smart manufacturing ecosystem. The IoT automation solutions are known for their connectivity and availability potential for various environments, which contributes to simplifying overall control. Let's figure out more details.
Smart Manufacturing: Promoting Agility
Increasing the flexibility of the enterprise associated with the introduction of cellular manufacturing. However, the limits of this technology make it insufficient for modern demands. It is the IIoT that brings the production to the point where it can be called Smart Manufacturing, or Factory 4.0. And that’s through its following benefits.
IoT Removes Wires
This contributes to increased flexibility at the physical level when deploying and scaling the production system. There are several IoT protocols and IoT network implementation options that are suitable for various production conditions, and hazardous and hard-to-reach areas. Wires need to be protected in dangerous zones, but this is not an issue within the wireless connection. Thus, it becomes much more convenient and resource-saving to connect new devices to an existing system and configure them via the cloud.
IoT improves Safety & Security
Manufacturing systems have strict security regulations, and IoT helps comply with them by implementing advanced worker safety IoT solutions, and security systems. Smart Manufacturing allows for creating systems with physical access protection, biometric login, motion detection, dangerous areas identification, and so on.
IoT Enhances Availability
Since configuring an FMS often requires specialized technical knowledge. It would be great to have an opportunity to perform these activities remotely, calling the corresponding people at a convenient time. By providing multi-level access to different employees, it will become much easier and faster to respond to incidents that can appear. Also, IoT simplifies setting up the updates for your production system and re-configure it in general.
IoT Expands the Room for Experiments
FMSs are quickly reprogrammed to off-the-shelf specifications but are also used for experimentation to determine which way to process, for example, a vehicle component, is optimal, or identify which model sells best. This is where the digital twin helps. By creating models of the manufacturing system and modifying the product in a digital version, you can immediately foresee all possible shortcomings of the future product. Another advantage of IoT is advanced analytics. By collecting data from products and machines, the IoT application helps you analyze and suggest the features that need to be improved in the manufactured product. Moreover, when you define that, it's easy to re-program the FMS to produce the updated version.
IoT Allows You to Get Rid of Scheduled Maintenance
The point is relevant for any production system, not only flexible ones. IoT shields against forced reactive maintenance by eliminating unexpected hardware failures. Having a machine at a glance, that is, having all the data reflect this status in real-time, you have all opportunities for predictive maintenance. You can schedule a service at the most convenient time and avoid cost-intensive downtimes.
Who Benefits from Smart Manufacturing?
As we mentioned above, the size of the company is not critical when it comes to implementing flexible solutions, but medium businesses that supply products to large players, directly need their products to be flexible. The ability to quickly adapt to new inputs is critical for highly specialized manufacturers. Their products can be highly valued, but due to their specificity, they cannot be in constant high demand. If considering the need for production expansion, it is beneficial for such companies to utilize existing capacities than to purchase fundamentally new equipment. Everyone who used to care about flexibility now gets a new round with Smart Manufacturing.
Flexibility is essential in the mass production of a small range of product sets. Regarding productions that rely on high-quality metal-based elements like the aerospace, medical, military, construction, and mining industries. The second branch who must develop its manufacturing systems with flexibility in mind, are producers of consumer goods, such as electronics and cars.
As we mentioned reshoring, it greatly simplifies logistics chains, which increases the flexibility window. Forced to reshore their manufacturing, many companies tend to take advantage of this. The opportunity to “test” their products by launching several versions might be among them.
How to Implement Smart Manufacturing?
Robots in production are far from new, but robotics can develop and improve the interconnections between physical and virtual worlds. When building a smart system, the very first thing that should always be in mind is its worship to custom business needs. We recommend considering the following practices:
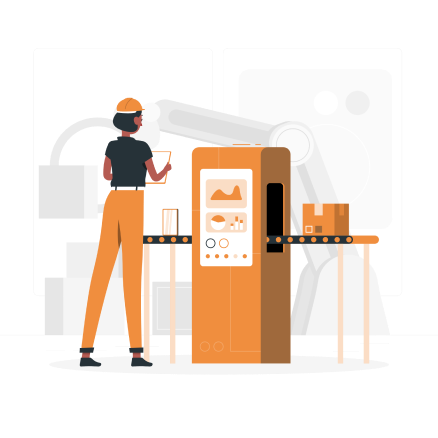
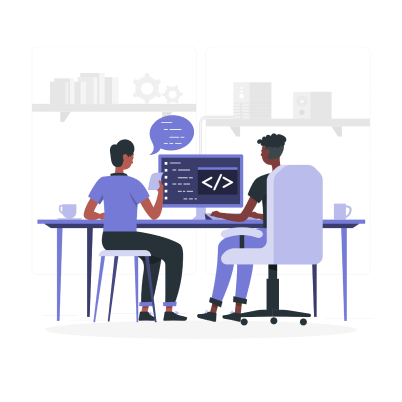
By knowing what exactly can be produced, and which modifications are possible for the product, you can create the optimal system that meets the needs of production. It is necessary to build it under verified KPIs.
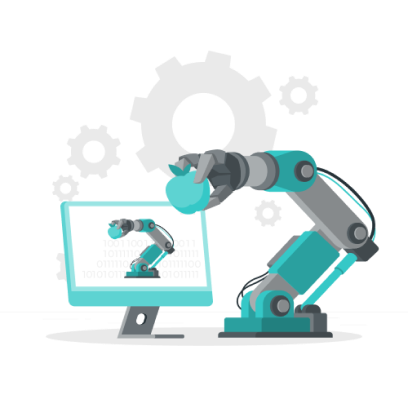
FSM implementation is often a serious financial investment, and even more so with an IoT component. Therefore, it is necessary to be sure that the system being developed meets all production parameters, and the digital twin will help in this best of all. It allows engineers to perform IoT testing of different versions of the product.
Conclusion about Smart Manufacturing
So, by implementing advanced FMS now, you have greater chances to:
- Adapt to an unknown future.
- Get the most out of your market by offering a variety of products.
- Optimize the production cycle.
- Run data-driven experiments.
Thus, Smart Manufacturing is impossible to imagine without flexibility. By investing in it now, you lay a reliable foundation for future enhancements.