Rail Maintenance: How to Establish a Predictive Approach?
In the rail industry, predictive maintenance (PdM) is often implemented only when issues with rail assets are glaringly apparent. For instance, when the bridge must be urgently closed for repairs, frequent breakdowns of level crossings become the subject of discussion by the general public. This approach leads to the fact that the company takes on a double financial burden – both for the urgent repair of the assets and for the development of an advanced solution for its maintenance. When making investment plans, it is more sensible to think ahead about predictive rail maintenance.
However, the conservative railway nature and the strict industry standards leave no experiment window and require any innovation to be firmly justified. As a result, PdM implementation can often be delayed even when the reasons for doing it are clear. The good news is that companies have enough data to correctly bring and justify a strategy for implementing predictive maintenance for their railway assets. Discover how to begin your journey, where to go, and which railway development services to use in this article.
Rail Maintenance – Where to Start Its Implementation?
Thanks to its speed, capacity, and convergence, the Internet of Things can now offer predictive maintenance for any rail asset in any environment, even if it is moving, hazardous, or hard to reach. It is crucial to prioritize the goals of implementing PdM before focusing on the means. Simply modernizing without accurately assessing your unique situation will not provide value.
The main objective of predictive maintenance is to extend the lifespan of an asset and minimize its maintenance expenses. Upgrades for the rail are often motivated by safety concerns. The PdM solution typically aims to achieve the following objectives:
- Targeted rail maintenance planning
- Timely inventory planning for replacement parts
- Identifying systems with poor performance for their further upgrades
- Increasing management transparency
To identify focus assets, research the most common causes of the failures/delays and the most capital-intensive assets on the railroad. To do this properly, connect your asset management system – a proper catalog of information describing the life cycle of assets, their components, regular service procedures, and spending. By following that process, you can determine precisely which equipment or parts require predictive maintenance first. It will also assist you in identifying the data collection methods and types. Although a minimum amount of data is required, make sure to use all available information when justifying the implementation of the innovation.
It makes sense to monitor the following assets: tracks, switches, signals, bridges, crossings, and tunnels. As we know from practice, about 20% of delays are caused by switch issues – so you can analyze these assets first.
Business Case for Shifting Rail Maintenance to Predictive Way
As you may know, effective asset management on the railroad is crucial. It can provide valuable data to support the implementation of PdM. For comprehensive data, it is important to include the life cycle of problematic assets, breakdown records over a specific period, and both quantitative and qualitative evaluations of the importance of each breakdown.
The estimated cost-effectiveness of predictive maintenance typically falls within a range of 12% to 25%. The benefits of using it may vary between industries, but they can be estimated with a relatively small degree of error. When preparing a business case, it is worth separately calculating the benefits for each goal you define. To illustrate, if your objective is to eradicate delays caused by a switch malfunction, you can compute the following:
This formula also allows you to derive the justified cost of the PdM solution. The formula can be adjusted for any set of assets, whether calculated individually or as a whole, to improve inventory management and efficiency. If possible, including third-party statistics and a forecast for the maintenance of aging equipment can strengthen the business case. Add the expected growing demand for rail transportation in your area, which must increase the reliability and availability of the infrastructure accordingly.
By now, you should have a grasp on how to incorporate predictive rail maintenance into daily asset management and coordinate it with resource planning.
Rail Maintenance: Assignment of KPI for Productive Tracking
To monitor the effectiveness of the IoT application, include rail maintenance Key Performance Indicators (KPIs) in the asset management plan (AMP). The AMP, in this case, should be a flexible document to adjust in the service management process.
Maintenance KPIs are defined as a percentage specifying the business goals. For example, you calculated that for a PdM solution to be cost-effective and profitable, you need to achieve the following KPIs within a year:
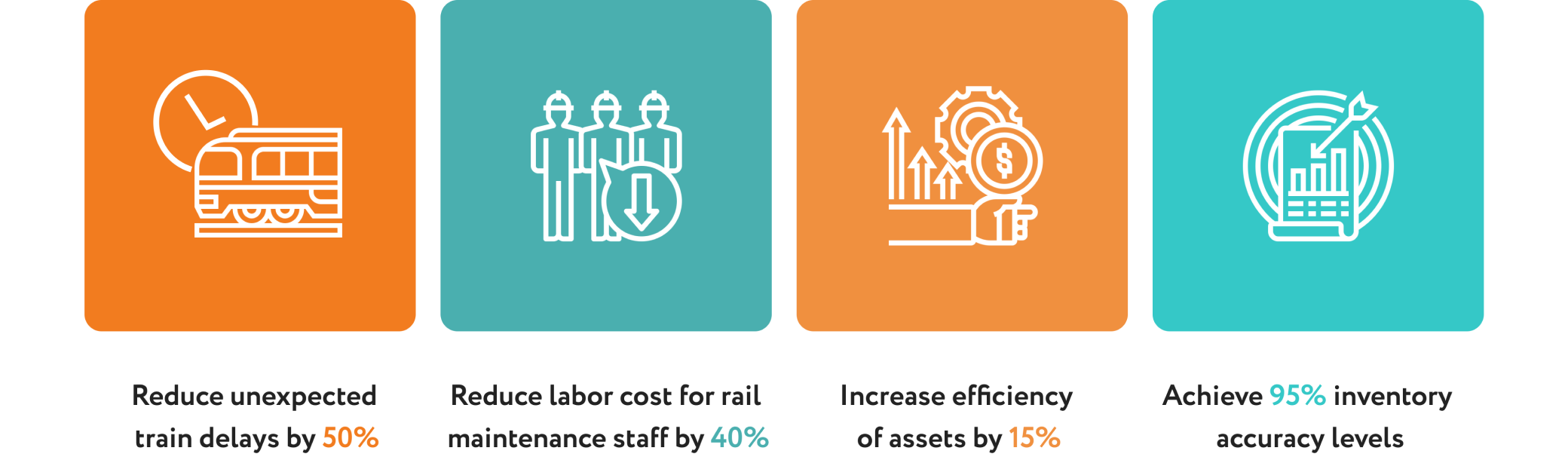
When setting KPIs, it is important to divide the goals into distinct sections and establish the relationship between the goal and a specific set of resources. Establish regular tracking periods to correct the plan if required. Thus, it would be clear where to move and what to fix if the intermediate results won’t meet the expectations.
Generally, it becomes a convenient tool for increasing the transparency of maintenance processes. The rail authorities can receive this information easily.
Rail Maintenance: Development of the Solution
Before you start developing a solution, you should determine, as confusing as it sounds, what you want to develop. The concept of predictive maintenance is often misused, implying that it only involves collecting data and providing real-time alerts. PdM, however, also involves complex deep analytics models that should track the issue long before its slightest visible hints appear. Since unpredicted downtime is critical for rail, it counts as justifiable to utilize predictive maintenance. But being its simpler alternative, condition-based maintenance might bring significant value too. If you're thinking about collecting and delivering data, it's a good idea to begin with condition-based rail maintenance, even if you plan to switch to predictive maintenance later. They both require substantial changes to the maintenance process, which can be too shocking for a conservative rail industry. Thus, it might be reasonable to start with a simple solution.
The components of the solution depend on the breadth of your goals first. The level of detail in the software, the amount of information stored, and the format used will depend on the purpose of data collection and the types of railway assets involved.
Comfortable minimum for the implementation of the solution for predictive maintenance includes the following:
- Hardware customization for real-time data collection. Remote sensors and edge computing are common tools here.
- Convenient software to display real-time data on assigned areas.
- Database connection
- Secure communications
- Communications with the staff and other interested parties.
Software development is crucial in this context. Creating a predictive maintenance tool can result in a centralized and easily accessible database containing valuable data on assets. Therefore, it is worth deciding to merge or connect databases and software to combine the info for asset management in one place.
If you are going to implement predictive maintenance, not simplified conditioning-based maintenance, you will need the help of data analysts to create optimal algorithms for your railway assets. Algorithms are derived from a detailed analysis of the behavior of each group of assets over a while. Special attention should be paid to this since false negative and false positive results in a rail situation can negate all the benefits of introducing predictive maintenance.
Recommendations for Implementing Predictive Solutions for Rail Maintenance:
Digital upgrades for many railroads start with the implementation of predictive maintenance. How rail companies use PdM tools plays a significant role in how they adapt to the future.
1. Implement PdM gradually
For highly structured and strictly regulated industries, it's recommended to start with condition-based maintenance and then exacerbate the solution with complex algorithms allowing for predictive maintenance.
2. Use the data Multilaterally
Having the data on assets and a proper asset management plan with future goals defined, you can negotiate new investments more effectively. Utilize data collected for predictive maintenance to drive innovations for your rail network.
3. Do not postpone maintenance when the issue is detected
The rail industry is highly regulated, which can make it difficult to adjust to flexible maintenance schedules. However, postponing maintenance procedures and combining them into regular schedules can be risky. It is critical to prioritize predictive maintenance, as the cost of planning maintenance is always lower in the long run.
4. Track the Results Regularly
Establish a time after which you will analyze the indicators of PdM solutions. This allows us to adjust some parameters to make a solution more successful.
You have been provided with crucial guidance on implementing predictive maintenance for your rail assets. The next step is to put this knowledge into practice. The PSA team is delighted to assist you in developing trustworthy PdM strategies that will enhance the efficiency and dependability of your rail system.