Digital model, digital shadow, and digital twin: their places in EIoT
It’s natural for humans to interact with physical objects. In fact, all of the artificial objects that surround us were designed with the idea to make them easier to interact with from the average human point of view.
“Predictably, digital copies of real objects began to appear with progress in IT virtualization. Due to the prevalence of CAD programs, 3D models have become an integral part of the modern design and development process.”
So there is no surprise that with the development of the IT technologies and progress in virtualization the digital copies or the real objects started to appear. Wide spread of CAD programs and 3D models created in them became an integral part of the new design and development process. In combination with mathematically simulated environments they allowed to evaluate the specs and design options of a new product in the “close-to-real-world” emulated conditions and did not require the physical prototype.
This approach evolved and resulted in the Digital model idea: when the parameters of the model and the real object were similarized so that the manipulations with the virtual object parameters produced the same result as if they were made with the real object and vice versa. Because there was no direct connection between digital and physical objects, the validation of the Digital model required countless manual operations of data transfer: changes, measurements and synchronization of parameters. A typical example of this is the aircraft design: you design the digital model, build the physical prototype, test it, then update the digital model until you get the desired result.
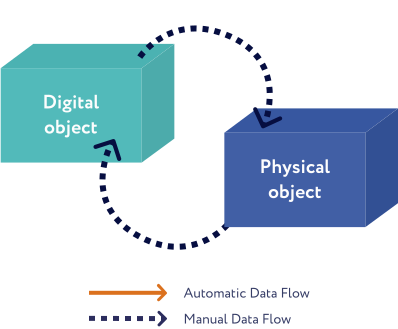
With the growing availability and affordability of different types of sensors , the Enterprise IoT solutions that once had limited use are now appearing in numerous everyday life objects. Those sensors were able to collect and report different data to the associated digital model automatically. The model in turn could be programmed to react to the data received and adjust the parameters according to the changes in the real object. This process, referred to as Digital shadow, is the one way automatic data flow from a real object to a digital model. It allowed us to collect historical data and, for example, by accelerating the time speed in the simulation environment to forecast (or predict) the future behaviour of the connected object from the physical world. The accuracy of the forecast was dependent on the model quality, the data amount collected. The digital instance was not able to communicate to the real object in real time due to the technological limitations. The example of the digital shadow was a telemetry system installed on F-1 bolids. The data from sensors was sent to the command center, analyzed by the tech team experts, and the recommendations were reported to the pilot.After the race, the data was then used for deeper analysis, simul
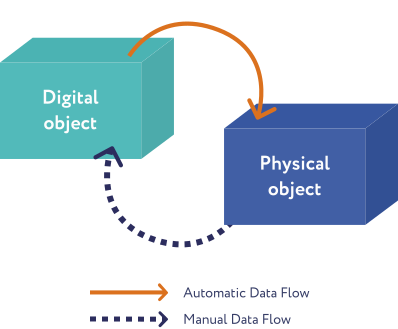
The next evolution was about analysis and usage of the data collected from the physical objects and real time automatic interaction with them on the basis of adaptive rules and policies. That became possible due to the significant progress in computing units and data processing speed, fast communication networks, neural networks and machine learning and forecasting algorithms implementation.
The new paradigm was called Digital Twin and it had fully automated data flow between the digital and physical objects. This approach means that the changes in state of the physical object lead to the changes in digital object and vice versa. Digital object can act as a primary instance with credentials to override the actions of the physical object. The example of Digital twin is Tesla cars, which are equipped with numerous sensors and a computer on the physical side that connects to the cloud backend which is constantly monitoring the state of the motors, battery, keeps firmware updated and is able to control automated functions of the car (like slowing down, acceleration and steering) if needed.
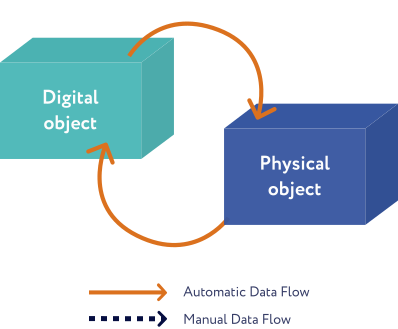
Digital twin - is the concept from the IoT world applied in both Consumer and Enterprise IoT segments. Any vertical inside EIoT can benefit from implementation of Digital Twin into standard analogue or semi-automated routines. Speaking of supply chain management and logistics, digital twins can be assigned to:
- Energy and Utilities: smart meters (multiple varieties)
- Healthcare: critical medical equipment
- Industrial automation: machines, tools and even the complete production facilities
- Smart buildings and cities: machines, tools and even the complete production facilities
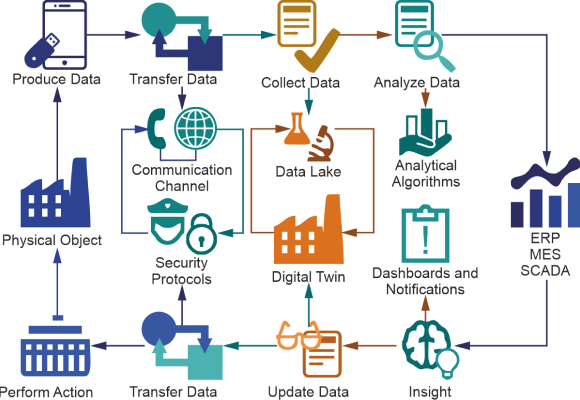
The most obvious (but not the only) benefits common to all mentioned industries:
- Avoidance of downtimes
- Implementation of predictive maintenance
- Selection of the optimal use mode for the equipment
- Automatic control override to prevent emergency issues
- Product lifecycle management
- Insights for new product development